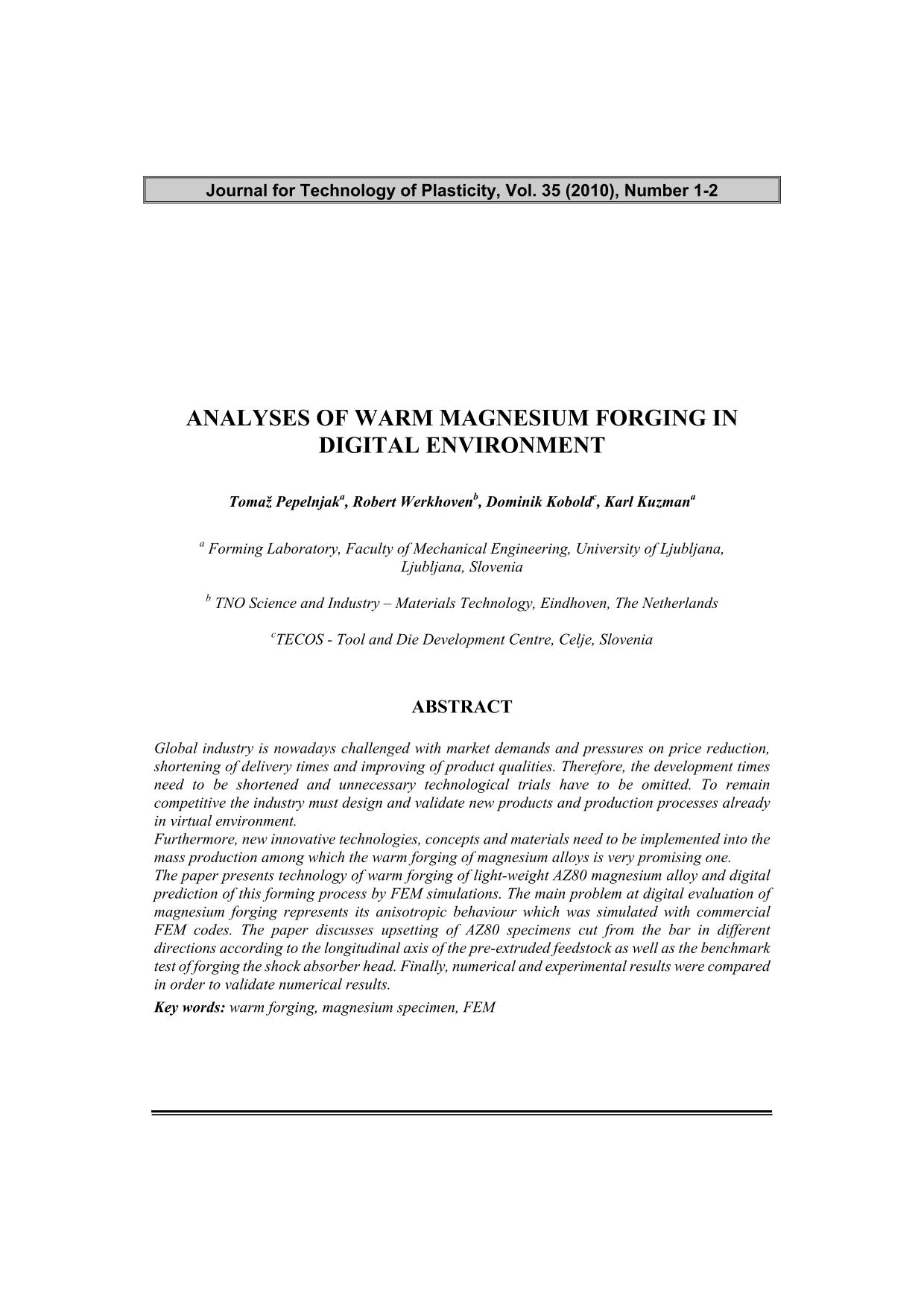
Published 2010-12-17
abstract views: 20 // Full text article (PDF): 9
Keywords
- warm forging,
- magnesium specimen,
- FEM
How to Cite

This work is licensed under a Creative Commons Attribution 4.0 International License.
Abstract
Global industry is nowadays challenged with market demands and pressures on price reduction, shortening of delivery times and improving of product qualities. Therefore, the development times need to be shortened and unnecessary technological trials have to be omitted. To remain competitive the industry must design and validate new products and production processes already in virtual environment. Furthermore, new innovative technologies, concepts and materials need to be implemented into the mass production among which the warm forging of magnesium alloys is very promising one. The paper presents technology of warm forging of light-weight AZ80 magnesium alloy and digital prediction of this forming process by FEM simulations. The main problem at digital evaluation of magnesium forging represents its anisotropic behaviour which was simulated with commercial FEM codes. The paper discusses upsetting of AZ80 specimens cut from the bar in different directions according to the longitudinal axis of the pre-extruded feedstock as well as the benchmark test of forging the shock absorber head. Finally, numerical and experimental results were compared in order to validate numerical results.