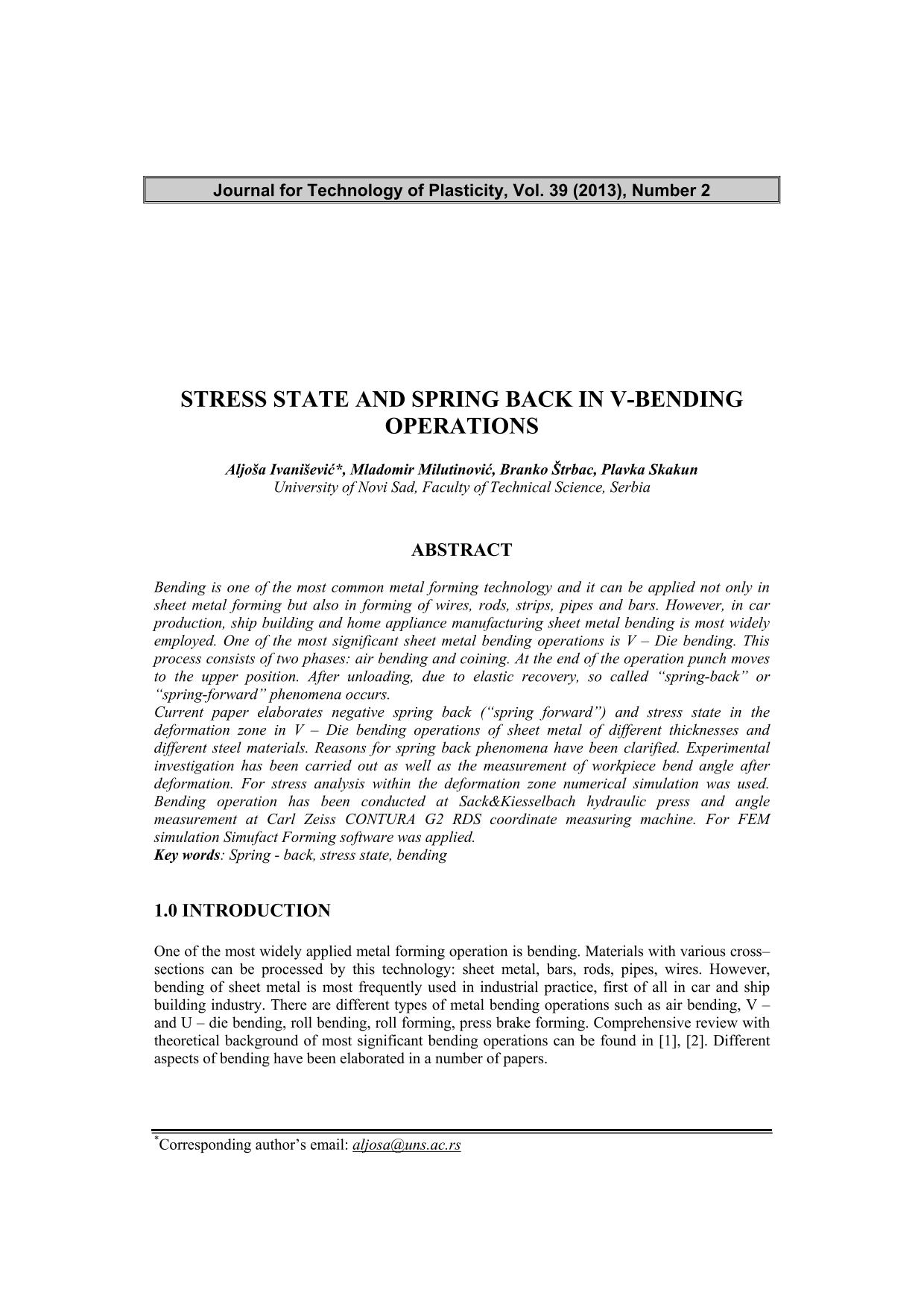
Published 2013-12-30
abstract views: 115 // Full text article (PDF): 33
Keywords
- Spring-back,
- stress state,
- bending
How to Cite

This work is licensed under a Creative Commons Attribution 4.0 International License.
Abstract
Bending is one of the most common metal forming technology and it can be applied not only in sheet metal forming but also in forming of wires, rods, strips, pipes and bars. However, in car production, ship building and home appliance manufacturing sheet metal bending is most widely employed. One of the most significant sheet metal bending operations is V – Die bending. This process consists of two phases: air bending and coining. At the end of the operation punch moves to the upper position. After unloading, due to elastic recovery, so called “spring-back” or “spring-forward” phenomena occurs. Current paper elaborates negative spring back (“spring forward”) and stress state in the deformation zone in V – Die bending operations of sheet metal of different thicknesses and different steel materials. Reasons for spring back phenomena have been clarified. Experimental investigation has been carried out as well as the measurement of workpiece bend angle after deformation. For stress analysis within the deformation zone numerical simulation was used. Bending operation has been conducted at Sack&Kiesselbach hydraulic press and angle measurement at Carl Zeiss CONTURA G2 RDS coordinate measuring machine. For FEM simulation Simufact Forming software was applied.