Numerical simulation of the plunge stage in friction stir welding alloys EN AW 2024 T 351 and EN AW 7049A T 652
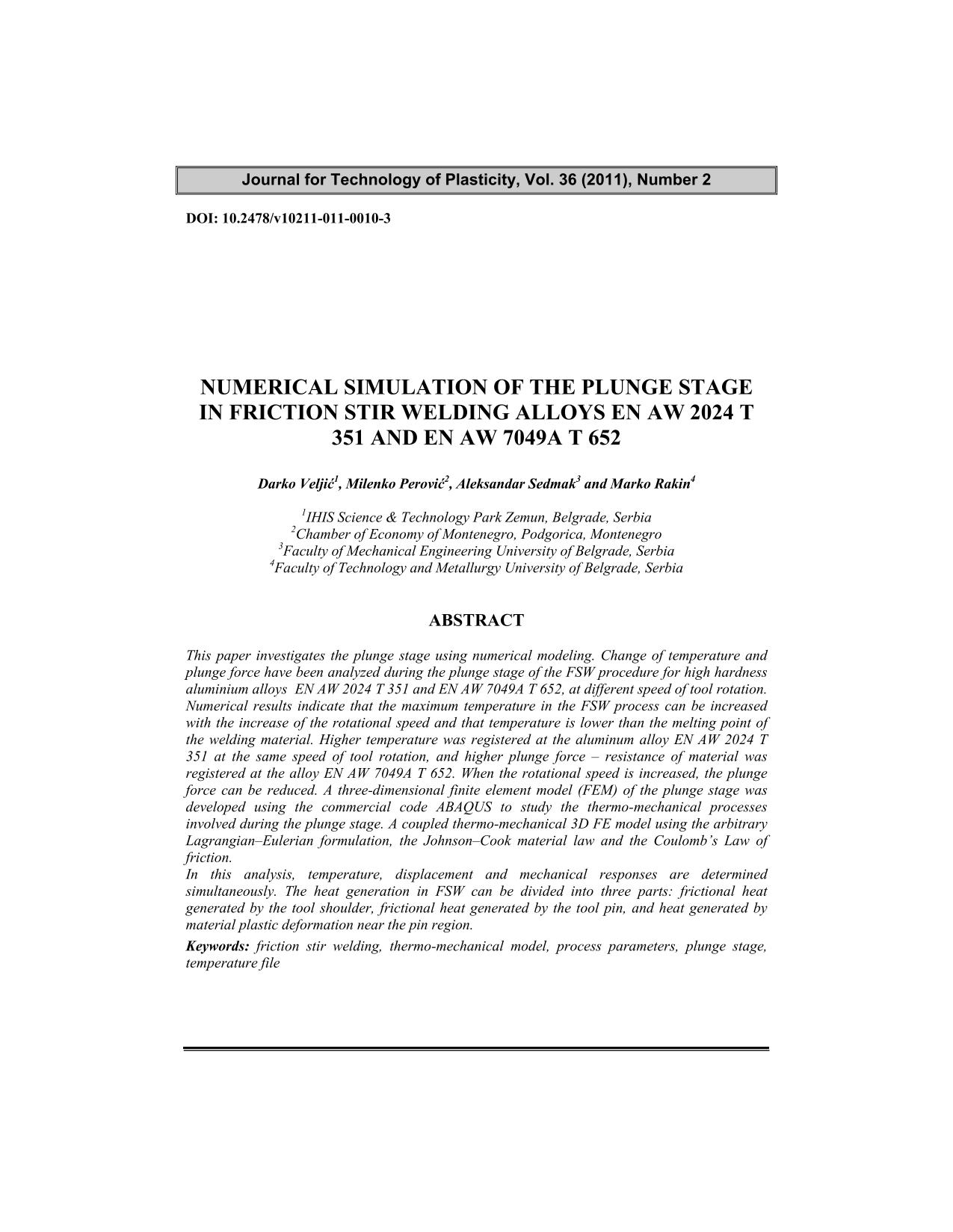
Published 2011-12-30
abstract views: 11 // Full text article (PDF): 7
Keywords
- friction stir welding,
- thermo-mechanical model,
- process parameters,
- plunge stage,
- temperature file
How to Cite
Copyright (c) 2011 This work is licensed under a Creative Commons Attribution 4.0 International License.

This work is licensed under a Creative Commons Attribution 4.0 International License.
Abstract
This paper investigates the plunge stage using numerical modeling. Change of temperature and plunge force have been analyzed during the plunge stage of the FSW procedure for high hardness aluminium alloys EN AW 2024 T 351 and EN AW 7049A T 652, at different speed of tool rotation. Numerical results indicate that the maximum temperature in the FSW process can be increased with the increase of the rotational speed and that temperature is lower than the melting point of the welding material. Higher temperature was registered at the aluminum alloy EN AW 2024 T 351 at the same speed of tool rotation, and higher plunge force – resistance of material was registered at the alloy EN AW 7049A T 652. When the rotational speed is increased, the plunge force can be reduced. A three-dimensional finite element model (FEM) of the plunge stage was developed using the commercial code ABAQUS to study the thermo-mechanical processes involved during the plunge stage. A coupled thermo-mechanical 3D FE model using the arbitrary Lagrangian–Eulerian formulation, the Johnson–Cook material law and the Coulomb’s Law of friction. In this analysis, temperature, displacement and mechanical responses are determined simultaneously. The heat generation in FSW can be divided into three parts: frictional heat generated by the tool shoulder, frictional heat generated by the tool pin, and heat generated by material plastic deformation near the pin region.