The improvement of friction bearing manufacturing technology by using copper alloy
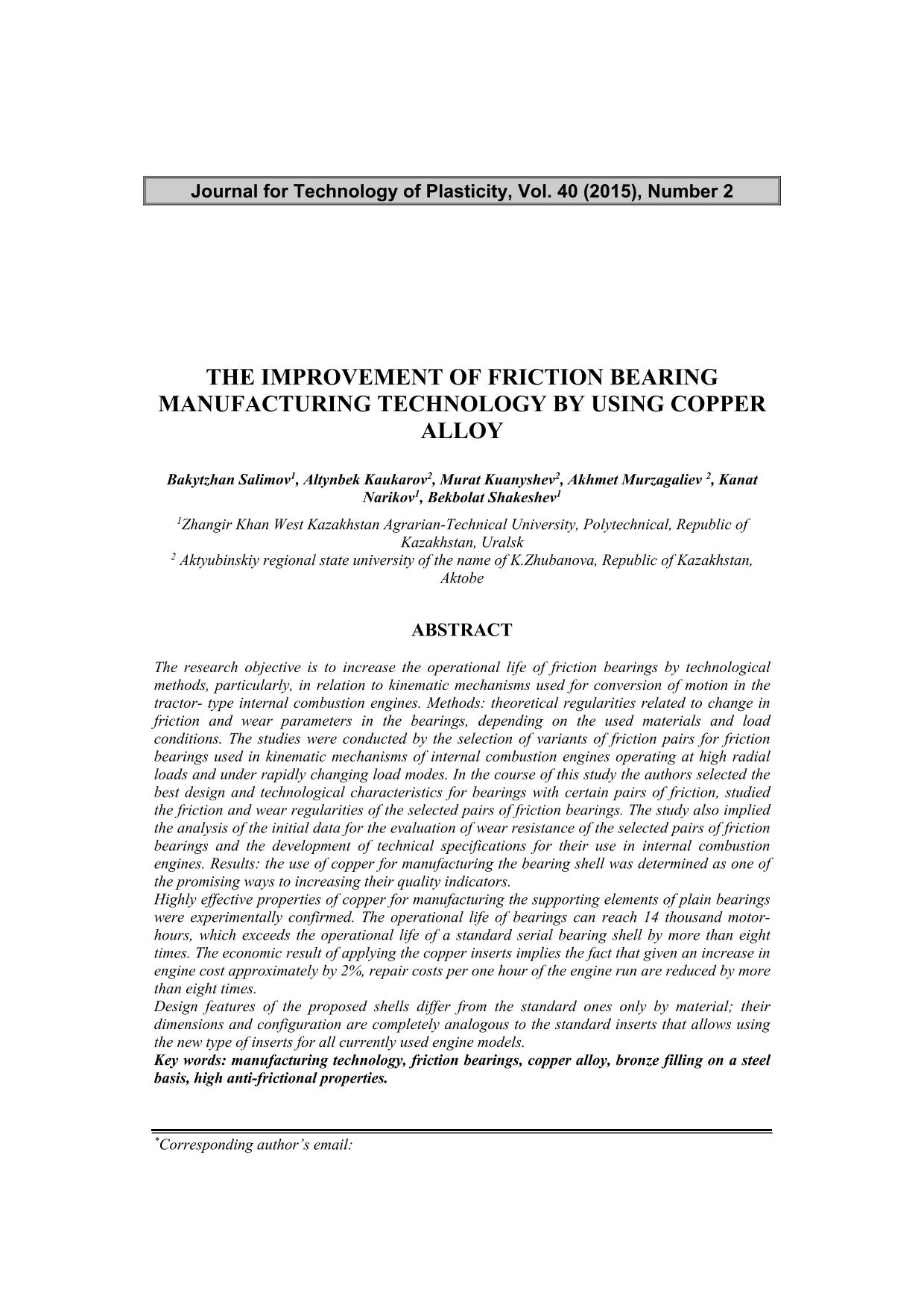
Published 2015-12-21
abstract views: 24 // Full text article (PDF): 0
Keywords
- manufacturing technology,
- friction bearings,
- copper alloy,
- bronze filling on a steel basis,
- high anti-frictional properties
How to Cite

This work is licensed under a Creative Commons Attribution 4.0 International License.
Abstract
The research objective is to increase the operational life of friction bearings by technological methods, particularly, in relation to kinematic mechanisms used for conversion of motion in the tractor- type internal combustion engines. Methods: theoretical regularities related to change in friction and wear parameters in the bearings, depending on the used materials and load conditions. The studies were conducted by the selection of variants of friction pairs for friction bearings used in kinematic mechanisms of internal combustion engines operating at high radial loads and under rapidly changing load modes. In the course of this study the authors selected the best design and technological characteristics for bearings with certain pairs of friction, studied the friction and wear regularities of the selected pairs of friction bearings. The study also implied the analysis of the initial data for the evaluation of wear resistance of the selected pairs of friction bearings and the development of technical specifications for their use in internal combustion engines. Results: the use of copper for manufacturing the bearing shell was determined as one of the promising ways to increasing their quality indicators.
Highly effective properties of copper for manufacturing the supporting elements of plain bearings were experimentally confirmed. The operational life of bearings can reach 14 thousand motorhours, which exceeds the operational life of a standard serial bearing shell by more than eight times. The economic result of applying the copper inserts implies the fact that given an increase in engine cost approximately by 2%, repair costs per one hour of the engine run are reduced by more than eight times.
Design features of the proposed shells differ from the standard ones only by material; their dimensions and configuration are completely analogous to the standard inserts that allows using the new type of inserts for all currently used engine models.