Advanced investigation on rapid prototyping techniques in maxillofacial surgery and implanting preparation
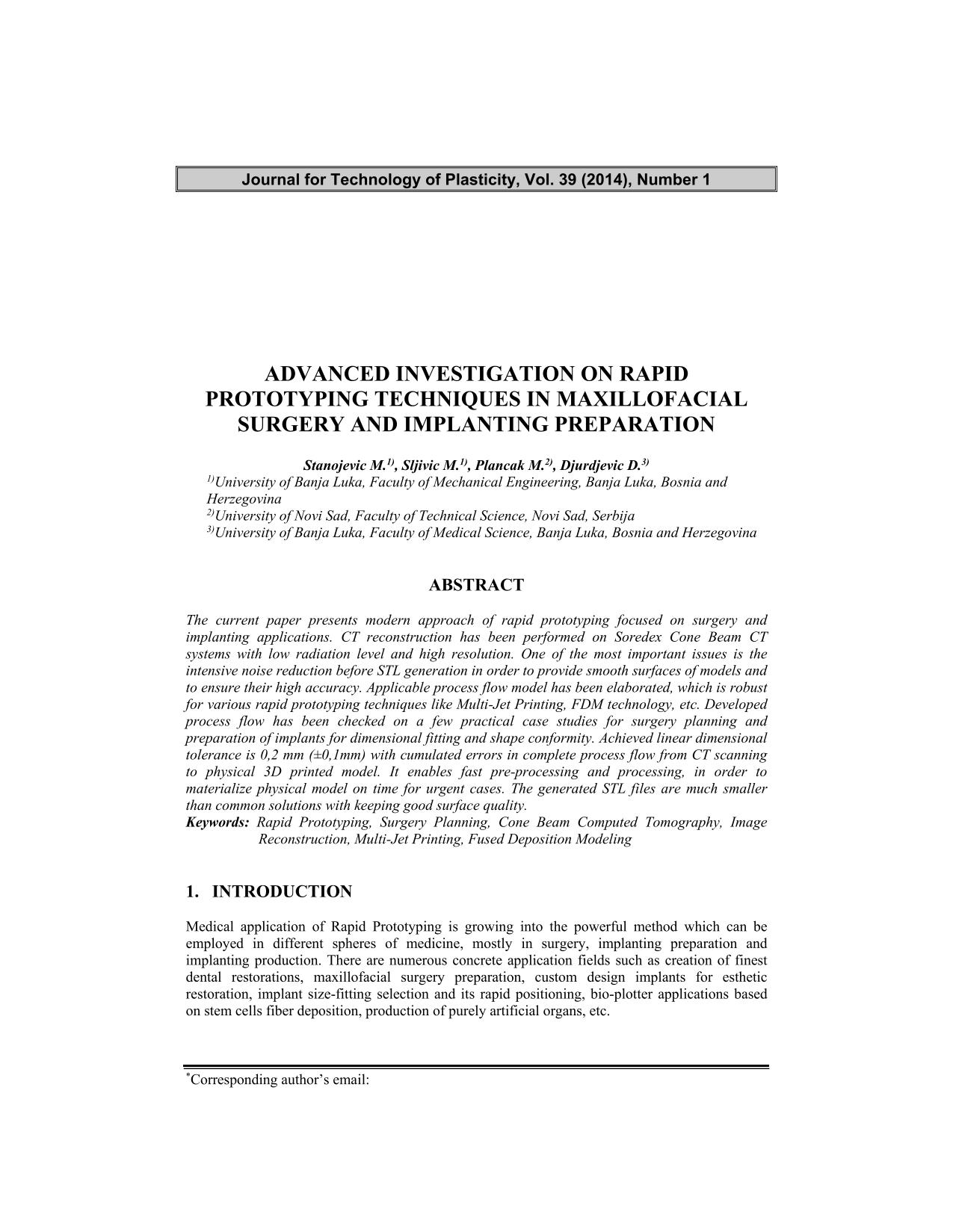
Published 2014-06-27
abstract views: 34 // Full text article (PDF): 0
Keywords
- Rapid Prototyping,
- Surgery Planning,
- Cone Beam Computed Tomography,
- Image Reconstruction,
- Multi-Jet Printing
- Fused Deposition Modeling ...More
How to Cite

This work is licensed under a Creative Commons Attribution 4.0 International License.
Abstract
The current paper presents modern approach of rapid prototyping focused on surgery and implanting applications. CT reconstruction has been performed on Soredex Cone Beam CT systems with low radiation level and high resolution. One of the most important issues is the intensive noise reduction before STL generation in order to provide smooth surfaces of models and to ensure their high accuracy. Applicable process flow model has been elaborated, which is robust for various rapid prototyping techniques like Multi-Jet Printing, FDM technology, etc. Developed process flow has been checked on a few practical case studies for surgery planning and preparation of implants for dimensional fitting and shape conformity. Achieved linear dimensional tolerance is 0,2 mm (±0,1mm) with cumulated errors in complete process flow from CT scanning to physical 3D printed model. It enables fast pre-processing and processing, in order to materialize physical model on time for urgent cases. The generated STL files are much smaller than common solutions with keeping good surface quality.