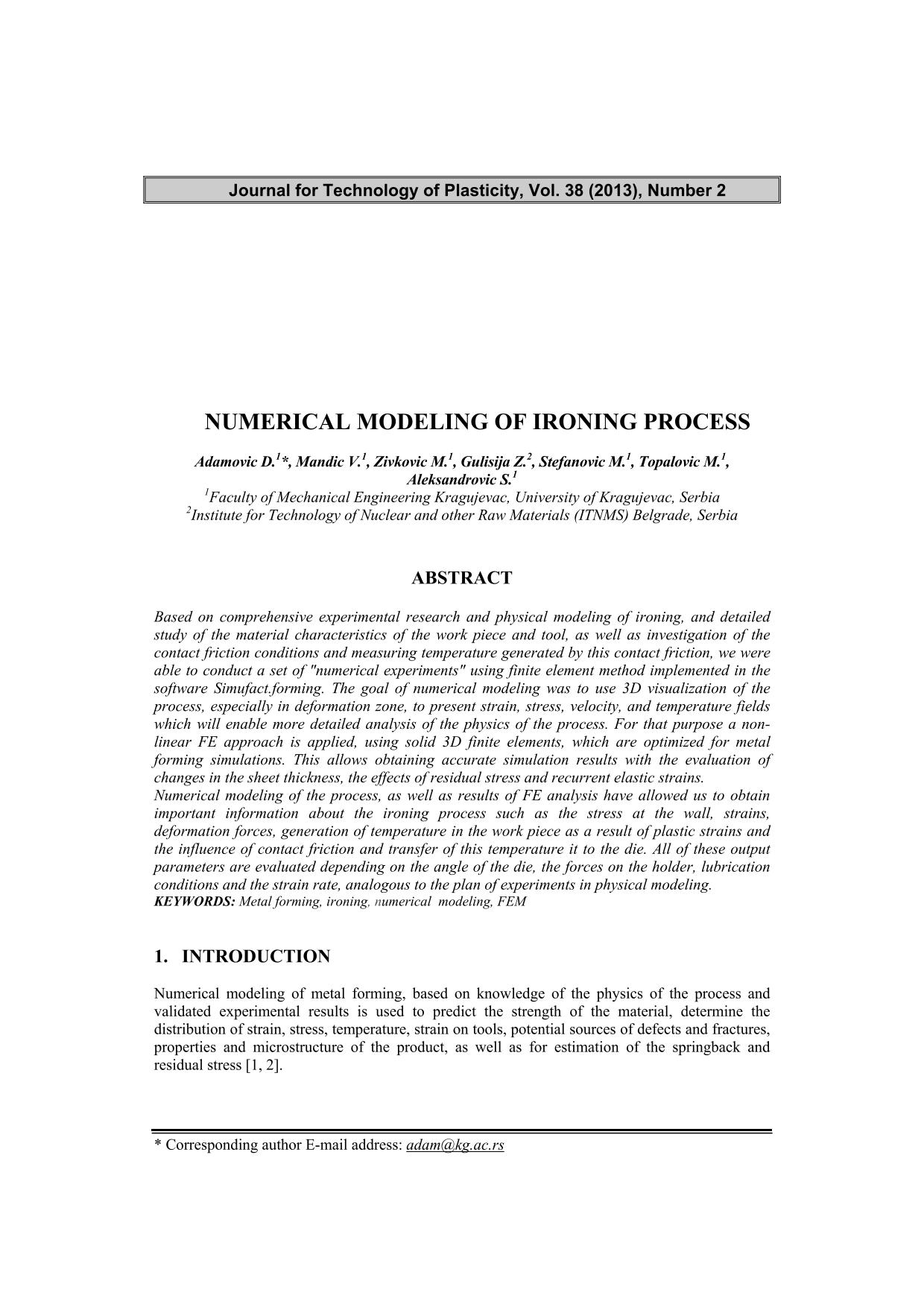
Published 2013-12-30
abstract views: 38 // Full text article (PDF): 18
Keywords
- Metal forming,
- ironing,
- numerical modeling,
- FEM
How to Cite
Abstract
Based on comprehensive experimental research and physical modeling of ironing, and detailed study of the material characteristics of the work piece and tool, as well as investigation of the contact friction conditions and measuring temperature generated by this contact friction, we were able to conduct a set of "numerical experiments" using finite element method implemented in the software Simufact.forming. The goal of numerical modeling was to use 3D visualization of the process, especially in deformation zone, to present strain, stress, velocity, and temperature fields which will enable more detailed analysis of the physics of the process. For that purpose a nonlinear FE approach is applied, using solid 3D finite elements, which are optimized for metal forming simulations. This allows obtaining accurate simulation results with the evaluation of changes in the sheet thickness, the effects of residual stress and recurrent elastic strains.
Numerical modeling of the process, as well as results of FE analysis have allowed us to obtain important information about the ironing process such as the stress at the wall, strains, deformation forces, generation of temperature in the work piece as a result of plastic strains and the influence of contact friction and transfer of this temperature it to the die. All of these output parameters are evaluated depending on the angle of the die, the forces on the holder, lubrication conditions and the strain rate, analogous to the plan of experiments in physical modeling.