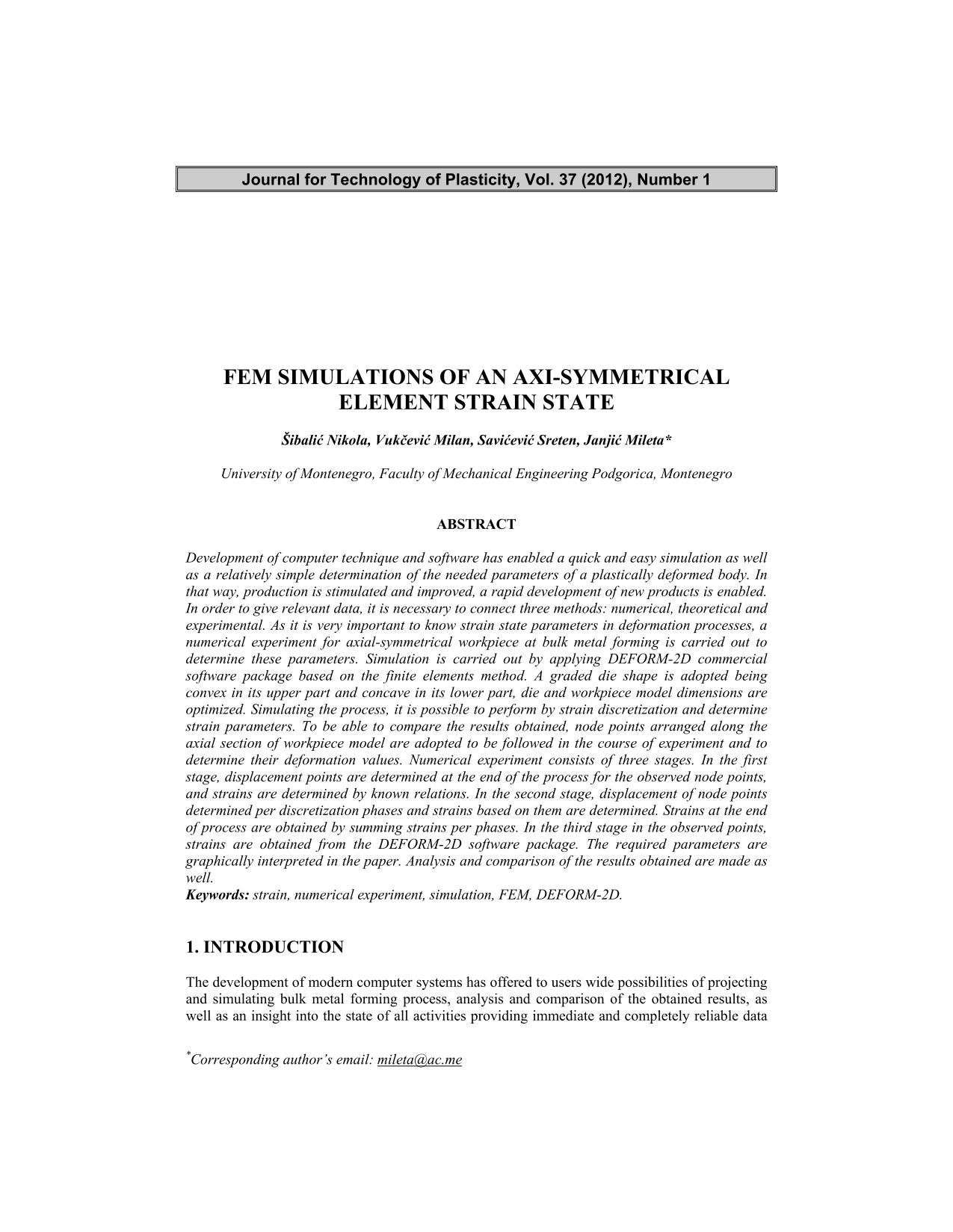
Published 2012-06-29
abstract views: 10 // Full text article (PDF): 4
Keywords
- strain,
- numerical experiment,
- simulation,
- FEM,
- DEFORM-2D
How to Cite

This work is licensed under a Creative Commons Attribution 4.0 International License.
Abstract
Development of computer technique and software has enabled a quick and easy simulation as well as a relatively simple determination of the needed parameters of a plastically deformed body. In that way, production is stimulated and improved, a rapid development of new products is enabled. In order to give relevant data, it is necessary to connect three methods: numerical, theoretical and experimental. As it is very important to know strain state parameters in deformation processes, a numerical experiment for axial-symmetrical workpiece at bulk metal forming is carried out to determine these parameters. Simulation is carried out by applying DEFORM-2D commercial software package based on the finite elements method. A graded die shape is adopted being convex in its upper part and concave in its lower part, die and workpiece model dimensions are optimized. Simulating the process, it is possible to perform by strain discretization and determine strain parameters. To be able to compare the results obtained, node points arranged along the axial section of workpiece model are adopted to be followed in the course of experiment and to determine their deformation values. Numerical experiment consists of three stages. In the first stage, displacement points are determined at the end of the process for the observed node points, and strains are determined by known relations. In the second stage, displacement of node points determined per discretization phases and strains based on them are determined. Strains at the end of process are obtained by summing strains per phases. In the third stage in the observed points, strains are obtained from the DEFORM-2D software package. The required parameters are graphically interpreted in the paper. Analysis and comparison of the results obtained are made as well.