Comparative studies on the microstructure and corrosion behaviour of forged and SLM processed 316L stainless steel
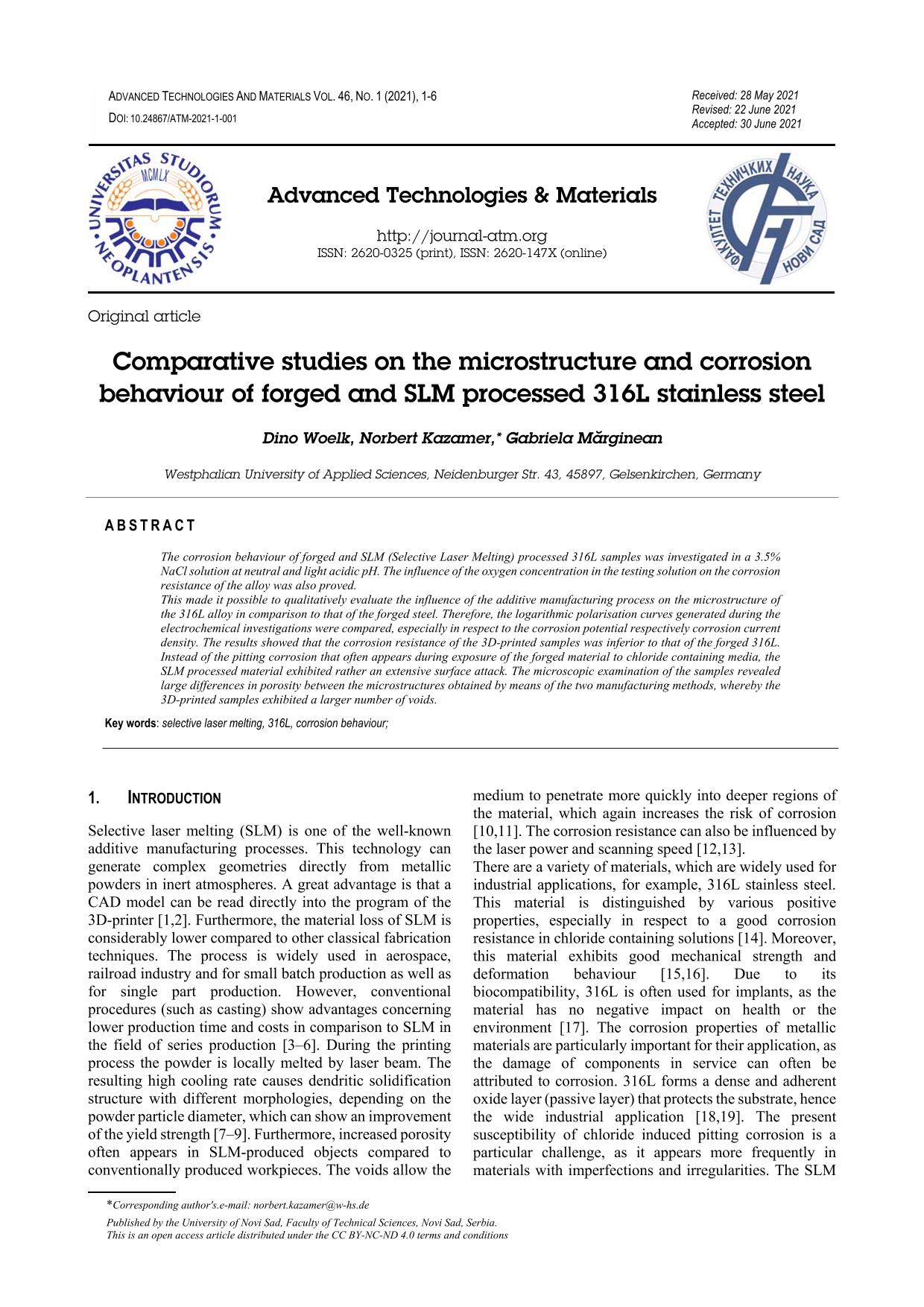
Published 2021-06-01
abstract views: 81 // Full text article (PDF): 50
Keywords
- selective laser melting,
- 316L,
- corrosion behaviour
How to Cite

This work is licensed under a Creative Commons Attribution 4.0 International License.
Abstract
The corrosion behaviour of forged and SLM (Selective Laser Melting) processed 316L samples was investigated in a 3.5% NaCl solution at neutral and light acidic pH. The influence of the oxygen concentration in the testing solution on the corrosion resistance of the alloy was also proved.
This made it possible to qualitatively evaluate the influence of the additive manufacturing process on the microstructure of the 316L alloy in comparison to that of the forged steel. Therefore, the logarithmic polarisation curves generated during the electrochemical investigations were compared, especially in respect to the corrosion potential respectively corrosion current density. The results showed that the corrosion resistance of the 3D-printed samples was inferior to that of the forged 316L. Instead of the pitting corrosion that often appears during exposure of the forged material to chloride containing media, the SLM processed material exhibited rather an extensive surface attack. The microscopic examination of the samples revealed large differences in porosity between the microstructures obtained by means of the two manufacturing methods, whereby the 3D-printed samples exhibited a larger number of voids.